Excerpts from the catalogue of the Königshütte mill construction institute from 1910
Mill construction has been an essential pillar of the Königshütte's operations since its privatisation in 1871. By 1930, entire mills between the Leine, Harz and North Thuringia had been equipped with facilities. Later, the company limited itself to the construction of roller mills. These can still be seen in some of the mills, which are still preserved in a museum today. In a catalogue from 1910 the machines offered at that time are shown:
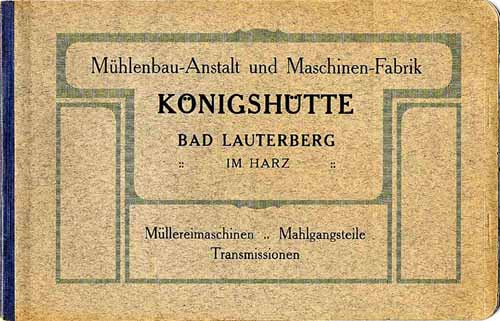
- The Aspirator
- The trieur
- The Roller mill
- The centrifugal separator
- The semolina cleaning machine
- The flour mixing machine
- Mill chairs
- The screw conveyor
- The elevator (bucket elevator)
The Aspirator
As the first machine in a grain cleaning system, an aspirator with sieve unit is highly recommended and is preferable to a sand and dust cylinder due to its excellent performance. With a completely dust-free operation, an aspirator with a bottom-mounted sieve unit removes all dust, clods, seeds, fireballs, dead grains, trespe, as well as coarser impurities such as stones, clumps of soil, beans, sack belts, etc. As soon as the grain enters the machine, it is subjected several times in succession to a powerful adjustable suction air flow, which removes dust and light particles. The grain then passes through a double sieve to separate coarser and finer impurities. After sieving, the grain passes through a suction air stream again, where all specific lighter particles are lifted and removed. The two suction air streams can be adjusted independently of each other. The dust sucked in by the fan is directed into a dust collector or a dust chamber.
The trieur
The illustration shows a trieurcylinder, as used in mills to separate the wheel, bird vetch, poppy and thistle seeds etc. from the grain. Inside the cylinder there is an adjustable catching trough in which the sorted seeds are collected and transported out of the machine. On request, a sieve can be installed at the inlet of the cylinder to separate sand, trespe, etc., which is advantageous in those cases where the grain is fed to the trieur without sufficient pre-cleaning. The installation is simple: you give the cylinder 80 mm drop on 1000 mm length and let the driving belt run directly on the cylinder. The cylinder rotates to the left when viewed from the infeed. If clockwise rotation is required, this must be specified when ordering.
The roller mill
Cereals -Pre-crushing -Roller mills
In view of the great advantages that a pre-crushing roller mill offers for the further grinding of the grain, such a machine should not be missing in any mill, especially since the purchase costs are not high. The dirt in the gap is loosened by lightly pressing the grains and can then be easily removed by a sieve or a brush screw with sieve. Furthermore, the husk is loosened from the actual endosperm, so that larger husks and lighter meal are obtained when the grains are crushed. The chairs are equipped with ring lubrication bearings, feed roller and wheels in the following sizes.
Shot roller mills
with Gruson hard cast iron rollers, automatic oil lubrication and disengagement, brushing device and bell.
A good purpose-built roller mill is indispensable in the smallest mill. In the construction of this important milling machine it is a basic condition that all parts are made of excellent material and that the design and construction is suitable for the intended use. In addition to a pleasing shape, we have taken care to reduce wear and tear of the moving parts, to arrange all components in a conveniently accessible and clearly arranged manner, and to make the operation simple and easy to understand. The base of the chair consists of a stable hollow cast iron housing on which the bearings for the rollers are mounted. The rollers are mounted in long two-part bearings with shells made of phosphor bronze, which are equipped with an oil chamber and automatic lubrication device. The upper part of the roller mill is equipped with double feed rollers, which ensure an evenly distributed feed of the material to be ground between the grinding rollers. The feed quantity can be regulated by means of an angle slide valve. The parallel adjustment of the rollers is carried out on both sides by means of handwheels, whereby it must be ensured that the pressure springs are not excessively tensioned, so that in the event of the passage of hard foreign bodies, the springs can still yield and the movable roller can yield. The rollers can be adjusted on a special handwheel spindle for deeper or higher grinding. A brushing device keeps the rollers clean. By virtue of a safe self-acting disengagement, the rollers move a few mm apart when the feed roller hopper is fairly empty. The differential speed of the rollers is provided by smoothly running spur gears with milled teeth, and both rollers can be set up with belt operation on request. We build chairs with rollers of 250, 300 and 350 mm diameter, the size, power and price of which are included in the table below. For wheat milling we recommend 250 mm diameter rollers, while for rye milling we prefer 300 and 350 mm diameter rollers. For wheat and rye milling on a chair, a roller diameter of 300 mm has proved to be the best.
Milling roller mills
with porcelain rollers, automatic disengagement and double feed roller.
The construction of these roller mills is carried out in the same solid way as for the shot roller mills. The porcelain sleeves used have a high degree of toughness and sufficient wall thickness to prevent the rollers from jumping. Due to the peculiar nature of the porcelain material, which provides a fine but sharply gripping grinding surface, and as a result of the different peripheral speeds of the rollers, the grits are ground lightly and loosely. The rollers require only little pressure, little operating force and deliver a light, non-slip flour. Special care has been taken in the wiper device for the porcelain rollers, because the good performance of the grinding rollers depends mainly on their correct function.
The centrifugal separator
Our centrifugal separators are characterised by high performance with low power requirements and low gauze consumption. We use first-class material for the machines, the construction is solid and clean, all parts are easily accessible. All bearings are two-part, with oil chamber and reliable filter lubrication. The material to be sifted is fed into the machine through a screw inlet mounted outside the machine housing, the material is discharged through openings in the casing disc at the outlet. Felt seals rubbing against the end walls of the machine, which cause the casing to run with difficulty, become leaky after a short time and allow particles of semolina and bran to fall into the flour, are avoided in the construction of our machines. Each machine is supplied with a set of frames covered with silk gauze and a set of un-covered frames.
The semolina cleaning machine
In the production of fine wheat flours, the cleaning of the semolina is extremely important; a good semolina cleaning machine should therefore be part of every mill that wants to produce good wheat flours. Our semolina cleaning machine is equipped with a vibrating sieve at the top, which divides the semolina to be cleaned into two types according to their size and feeds them into the cleaning boxes located below. In the cleaning boxes, the grits pass through several inclined surfaces lying above and behind each other, whereby they are continuously exposed to an adjustable suction air stream, which separates flying bran etc. and separates the grits into three types according to their quality and weight. The machine cleans the grits completely in a single pass. On request, the machine can be equipped with a feed roller, which is useful in cases where the machine is manually tipped.
The flour mixing machine
In this machine the flour is mixed to perfection without any pressure. In many other systems the flour is compressed by the pressure before mixing, but compressed flour can never mix intimately, as any expert knows. In this machine, the mixing process is carried out by lifting the flour from one roller and pulling it down from the other. The different types of flour are then loosely rubbed together, finely distributed in the collecting auger and mixed in the most thorough way. It is precisely this trituration, which is missing in other systems, that is essential for intimate mixing of the flour. As the rollers move and the flour stored above them stands still, only a thin layer, which just touches the rollers, is set in motion at any given moment. This layer now undergoes the same process as the ground material in the grinding process between the rotor and the bottom stone, in that the stationary superimposed flour corresponds to the soil, but the moving rollers correspond to the rotor. By rubbing the different flours together, a single new type of flour is produced in which, even after careful examination, the individual components can no longer be detected separately. The many repeat orders and the large number of machines in operation prove that the machine performs excellently. The machine can be fed either by the upper auger, or from a floor below by an infeed auger to the elevator. It does not matter in which order the flour enters the machine, if only the container contains all the varieties to be mixed. Depending on the local conditions, the mixed flour can be bagged either directly from the upper or lower auger, or from an intermediate floor. In most cases the upper flour container is made on site by a millwright or carpenter, unless otherwise agreed, it is excluded from our delivery.
Mill chairs (for grinding processes)
To achieve high efficiency and good operation of a grinding process, a solid and functional design of all operating parts as well as smooth running of the drive wheels is essential. On the basis of many years of practical experience gained during the delivery of hundreds of these chairs, we have taken the above conditions into special consideration when designing the individual parts and have created various mill chairs that meet all requirements with easy access, stability and clean design. We supply mill spindle trestles in various sizes and designs suitable for conical applications. Gear drive, spur gear or belt drive of the grinding gears, suitable for all possible conditions.
The screw conveyor
The elevator (bucket elevator)
The design of our elevators with adjustable bearings and side doors at the elevator foot has proven itself in practice. In the bottom of the elevator foot there is a slide for emptying. The bonnet of the head is designed to be removed. We supply elevators for lifting grain, all kinds of ground material, minerals, ice, etc. A complete iron set consists of: 2 belt pulleys with shafts and adjusting rings, 4 bearings with ring lubrication or with stauffer bushes and 1 drive pulley A complete elevator head and foot consists of: 1 complete iron set connected to a wooden head and foot. For other dimensions not shown in the table, as well as for all iron elevators, we are at your disposal for estimates.